Von der Magnettafel zum Echtzeit-Dashboard
Pankl Racing Systems AG
Herausforderungen
Digitale Echtzeit-Abbildung der Produktion trotz großer Datenmengen
Lösung
Zentrale Darstellung der aktuellen Produktionsdaten auf einem Peakboard Andon Board
Vorteile
- Verbesserte Planung und Logistik
- Echtzeit-Darstellung erlaubt gezielte Ursachenanalysen bei Problemen
- Überblick über aktuelle Aufträge und Sollvorgaben, die aktuelle Stückzahl, den prozentualen Fortschritt, den Maschinenstatus und Gründe für Maschinenstillstände
Time to Value
Wenige Tage bis zum Echtzeitdashboard
Die 1985 gegründete Pankl Racing Systems AG ist ein international führender Hersteller von mechanischen Systemen im Hochtechnologiebereich für dynamische Komponenten in den weltweiten Nischenmärkten der Rennsport-, Luxusautomobil- und Luftfahrtindustrie. An weltweit sieben Standorten betreuen 2.200 Mitarbeiter Kunden wie Ferrari, Porsche, McLaren und Airbus.
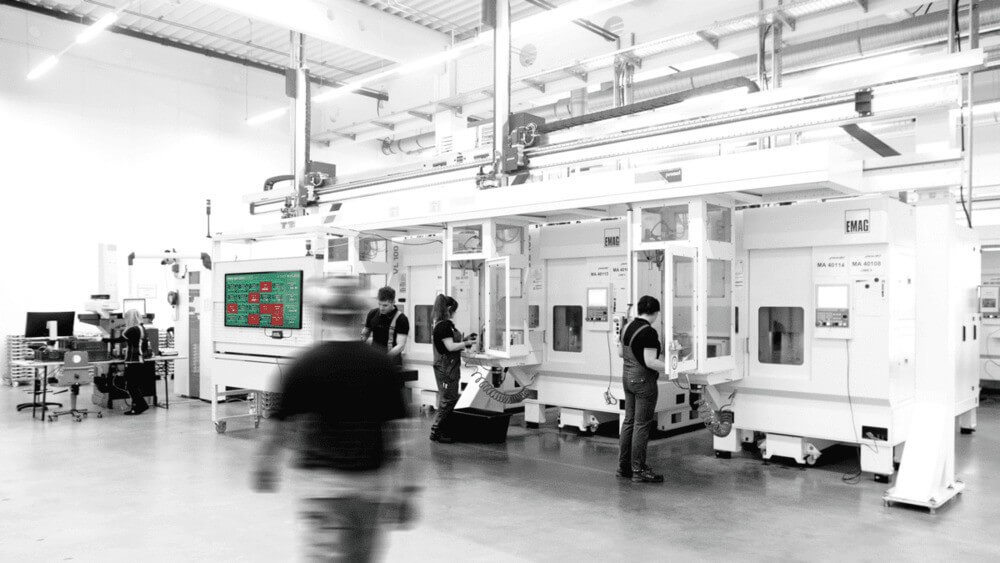
„Wir brauchten eine zentrale Darstellung der aktuellen Produktionsdaten auf einem Andon Board, um den nächsten großen Schritt zur Operational Excellence zu gehen. Mitarbeiter sollten in Echtzeit den Status ihrer Anlage sehen können: Was läuft hier und jetzt auf meiner Maschine? Die auszuwählende Lösung sollte außerdem zum Standard in unserem Konzern werden können, um nicht mit einer großen Anzahl verschiedener Systeme zu arbeiten.“
Kompliziert war gestern
In der Produktion gibt es eine Magnettafel mit ausgedruckten Listen, in die die Mitarbeiter im Zweistunden-Takt händisch den Produktionsfortschritt eintragen. Bei Schichtende wird diese Liste an die Produktionsplanung übergeben und in Excel übertragen. Lediglich Schicht- und Produktionsleiter erhalten eine visuelle Aufbereitung der Daten. Eine Analyse der Ursachen von Verzögerungen findet im Nachhinein und damit verspätet statt und ist nicht immer zielgenau. Darüber hinaus ist dieses System aufwendig und fehleranfällig.
Im Laufe des Entscheidungsprozesses kristallisiert sich heraus, dass die Lösung auch MES-Eigenschaften aufweisen soll. „Die bisher im Unternehmen eingesetzten Systeme waren nicht flexibel genug und ermöglichten keine interaktiven Eingaben. Dadurch waren die Daten nicht aktuell, wir konnten nicht agil planen und die Mitarbeitenden im Schichtbetrieb hatten bei Schichtende keine Kenntnis des aktuellen Tagesstandes der Produktion“, erklärt Jordan Marlin, Manager Operational Technology, Industry 4.0 Engineering bei BWI.
Flexibel und agil
Das Unternehmen strebt nach einem möglichst geringen personellen und finanziellen Aufwand bei der Datenanbindung und-visualisierung. Weitere Kriterien sind die Flexibilität und die Unabhängigkeit vom Partner.
„Es sollte einfach und schnell umsetzbar und inhouse leicht anpassbar sein, ohne IT-Ressourcen zu beanspruchen“, fasst Pichler zusammen.
Das Team testet mehrere Angebote, die sich als zu kompliziert erweisen und umfangreiche Schulungen erfordern.
„Bei Peakboard hingegen konnte ich kostenlos den Peakboard Designer downloaden und alles sofort testen, auf Aussagen von Verkäufern oder Produktdemos war ich nicht angewiesen. Die bereitstehenden Templates zeigten dann schon sehr deutlich, was möglich ist“, sagt Pichler. „Bis ins Scripting hinein habe ich nachvollzogen, wie Aufgaben gelöst wurden, obwohl ich von Haus aus kein Programmierer bin. Wo ich konkrete Unterstützung brauchte, war der Support sehr hilfsbereit, auch schon bevor wir zum Kunden wurden.“
Von der ERP über eine SQL-Datenbank ins Dashboard
Pankl beginnt damit, durch sein Business Application Team die Datenbasis herzustellen und eine SQL-Datenbank zu programmieren, um nicht direkt auf das ERP zugreifen zu müssen. Seitens der IT stellt dies die bevorzugte Lösung dar, da sie die Daten jetzt in ein separates System einspielen kann und selbst ab diesem Punkt nicht mehr involviert ist. Die zu verarbeitende Datenmenge umfasst etwa 15.000 Zeilen, die das Unternehmen vorab reduziert. Mehr als die Hälfte des Dashboards designt Pichler direkt selbst, für den Rest führt Pankl einen Workshop mit Peakboard durch.
Aktuell sind an zwei Standorten insgesamt sechs Peakboard Boxen und viermal Peakboard Edge installiert, die 20 Produktionslinien beziehungsweise -prozesse digital abbilden und auch das Einspeisen von Informationen erlauben, die noch nicht digital vorliegen. Die Mitarbeiter sehen den aktuellen Auftrag und seine Sollvorgabe, die aktuelle Stückzahl, den prozentualen Fortschritt, den Maschinenstatus und auch die Gründe für Maschinenstillstände, die über eine interaktive Eingabemaske im ERP auf das Dashboard gelangen. Die Displays befinden sich, zentral erhöht montiert, im jeweiligen Produktionsabschnitt und aktualisieren alle zehn Minuten die Daten, die die Mitarbeiter auch aus dem Homeoffice abrufen können. Ein Mainscreen gibt einen Überblick, drei Teilscreens ergänzen die Informationen mit wichtigen Details.
Die Vorgesetzten und Betriebsleiter sind von dem System sofort überzeugt.
„Wir waren so begeistert von den Möglichkeiten, dass wir 25 Visualisierungen auf einem Screen nacheinander durchblättern ließen. Peakboard hatte uns davon abgeraten, aber wir wollten es einmal ausprobieren“, beschreibt Pichler die ersten Gehversuche. „Das war überladen. Unsere Leute mussten lange warten, bis sie ihre Maschine sehen konnten. Jetzt haben wir eine Visualisierung, die sofort und so groß wie möglich den Status quo der wichtigsten Parameter anzeigt.“
Das trifft den Bedarf der Schichtleiter, die jetzt auch aus der Ferne die für sie notwendigen Informationen jederzeit auf einen Blick erkennen können.
„Hätten wir diesen Fehler bei einer klassischen Lösung begangen, wäre es ein kostenintensiver Prozess geworden. Jetzt war das Problem nach einem halben Tag Anpassung inhouse behoben, ohne die IT beanspruchen zu müssen.“
Agilere Prozesse durch vollständige Transparenz
Die Mitarbeitenden von Pankl wissen seit über einem Jahr minutengenau, ob sie on- oder off-track sind. Unterbricht eine Linie, können sie sofort eingreifen. Vor der Lösung musste ein Mitarbeiter ungefähr 15 Minuten lang die Stehzeit einer Maschine per Hand abschreiben und weitergeben. Zudem haben sich Planung und Logistik deutlich verbessert und die Echtzeit-Darstellung erlaubt gezielte Ursachenanalysen.
„Die Schichtleiter können schneller auf Abweichungen reagieren. Bei 20 Anlagen und 10.000 m² Produktionsfläche ging die Übersicht verloren. Jetzt sieht man auf einen Blick die gesamte Produktion am Mainscreen. Technischer Leiter, Betriebsleiter und Planung können per Peakboard Hub auf die Daten zugreifen und haben ebenfalls Einblick in den aktuellen Produktionsfortschritt. Unser Schichtreport wird anhand der Daten automatisch erstellt und per Mail verteilt. Da wir 24/7 produzieren, sind diese Informationen für die Führungskräfte äußerst wichtig“, zieht Pichler ein positives Fazit.
Pankl reflektiert daher, das System sukzessive auf weitere Standorte und Tochterunternehmen auszuweiten, um es als konzernweite Standardlösung zu etablieren.
Starte jetzt mit Peakboard und vereinfache deine Prozesse
Verwandle Live-Daten in smarte Entscheidungen – mit Peakboard.