Echtzeit-Datenvisualisierung für eine höhere Produktivität

MUNSCH Kunststoff-Schweißtechnik GmbH
Herausforderungen
Digitale Visualisierung des Bearbeitungsstatus von Reparaturen in der Werkstatt
Lösung
Einführung von Peakboard zur Informationsvisualisierung über zwei unterschiedliche Screens per 65-Zoll-Monitor
Vorteile
- Wegfall des bisherigen manuellen Aufwands für die Visualisierung des Prozessfortschritts bei Reparaturen
- Medienbruchfreie Umsetzung von der Datenerhebung bis zur Visualisierung
- Schnelle Erfassbarkeit der Informationen über einen zentralen Monitor in der Werkstatt
Time to Value
Ein Tag bis zur Bereitstellung eines lauffähigen Dashboards mit zwei verschiedenen Screens
Die MUNSCH Kunststoff-Schweißtechnik GmbH ist seit rund 40 Jahren auf die Herstellung handhabbarer Werkzeuge zum Schweißen thermoplastischer Kunststoffe spezialisiert und gilt heute als weltweit führender Anbieter. Entwickelt, produziert und geprüft werden die Produkte in Ransbach-Baumbach im Westerwald. Zum Einsatz kommen die Kunststoff-Handschweißextruder und Heizkeil-Schweißmaschinen in aller Welt.
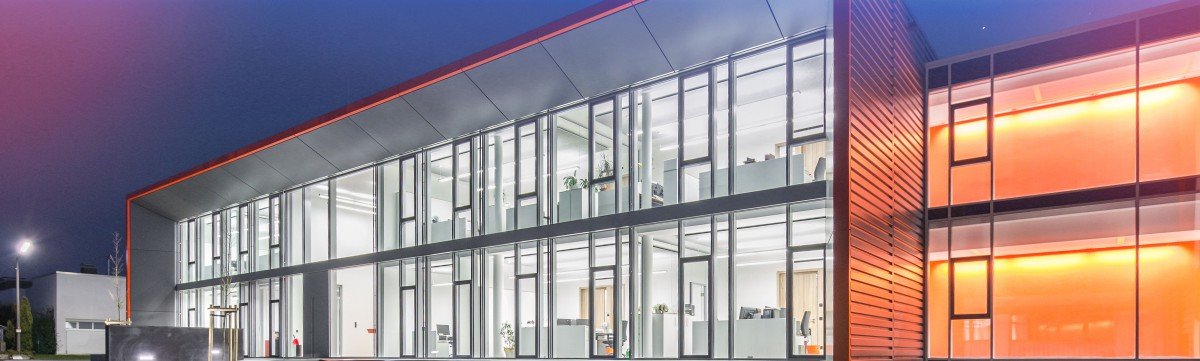
„Mit Peakboard haben wir Effizienz durch mehr Transparenz erreicht. Die Mitarbeiter können mit einem Blick direkt am Arbeitsplatz erfassen, wie der aktuelle Status ist und ihre Arbeitsschritte entsprechend lenken.“
Mehr Transparenz im Prozess
Neben der Produktion gehört zum Leistungsspektrum des Familienunternehmens die Reparatur dieser Geräte.
Um den Reparaturprozess im Sinne von mehr Effizienz und einer höheren Kundenzufriedenheit zu automatisieren, wurden die verschiedenen Prozessschritte digitalisiert. Abgebildet wurde der gesamte Prozess von der Einreichung des defekten Extruders, der Analyse des Reparaturbedarfs, der Erstellung des Kostenvoranschlags (KV) und Zusendung an den Kunden über die Veranlassung der Reparatur nach freigegebenem KV bis hin zu Verpackung/Warenausgang des reparierten Geräts. Die Buchung der einzelnen Schritte erfolgt gestützt durch Barcodes und entsprechende Scanner durch die Mitarbeiter in der Werkstatt.
Im nächsten Schritt folgte die Visualisierung der Informationen.
„Gestartet sind wir mit einem sogenannten Card-Board, einer Magnettafel, auf der die verschiedenen Stadien des Reparaturprozesses abgebildet sind. Jeder Reparaturauftrag wurde auf einer Art Visitenkarte abgebildet, ausgedruckt, an das Card-Board gehängt und dort je nach Bearbeitungsstatus weitergeschoben. Das Board war aber so gut wie nie aktuell, weil das Umhängen der Reparaturkarten zu spät oder gar nicht erfolgte. Das eigentliche Ziel, für mehr Transparenz im Prozess zu sorgen, haben wir mit dieser Methode verfehlt“, erläutert Oliver Herz, Leiter Anwendungsentwicklung bei der MUNSCH-Unternehmensgruppe.
Der Medienbruch zwischen der digitalisierten Erfassung der Prozessschritte und dem manuellen Verfahren, den Prozessfortschritt zu visualisieren, sollte durch die Einführung einer digitalen Visualisierungslösung aufgehoben werden.
Blitzschnell zum ersten Dashboard
Auf die richtige Fährte brachte Oliver Herz der eigene Chef. Er brachte die Visualisierungslösung der Peakboard GmbH ins Spiel – eine installationsfreie All-in-One-Lösung in Gestalt einer WLAN-fähigen, Smartphone-kleinen Aluminiumbox mit vollständiger Technologie für die Aggregation von Daten aus verschiedensten Quellen und deren Visualisierung in Echtzeit. Ein zentraler Server ist nicht erforderlich, da Peakboard die Daten selbstständig visualisiert. Peakboard greift über WLAN oder LAN direkt auf eine Datenquelle, zum Beispiel ein ERP- oder Lagerhaltungsprogramm zu, aggregiert die Daten für die Visualisierung und überträgt sie über ein HDMI-Kabel an den gewünschten (Groß–) Bildschirm, beispielsweise in der Produktionshalle. Daten und Visualisierungen können jederzeit eigenständig, ohne externen Support per PC oder Notebook angepasst werden.
„Ich hatte noch nie von dieser Lösung gehört und habe mich erstmal im Internet schlau gemacht. Die Idee hinter dem Produkt hat mich begeistert.“
Binnen nur eines Tages hat der leitende Anwendungsentwickler der MUNSCH-Unternehmensgruppe ein Dashboard mit zwei Screens für den Einsatz in der Werkstatt entwickelt und umgesetzt.
„Der Support seitens Peakboard war ebenfalls sehr gut“, ergänzt Herz. „Die Antwortzeit bei Fragen liegt bei unter einem Tag. Was mir auch gefallen hat: In der Einführungszeit hat der Support regelmäßig proaktiv nachgefragt, ob es Unterstützungsbedarf gibt.“
Visualisierungen mit Wow-Effekt
Als Datenbasis fungiert das auf Microsoft SQL Server basierende ERP-System APplus. Die Aktualisierung der Tabellen, auf die Peakboard zugreift, erfolgt alle fünf Minuten. Als Bildschirm kommt ein 65-Zoll-Monitor zum Einsatz.
Visualisiert wird der chronologische Wareneingang reparaturbedürftiger Extruder. Der Mechaniker kann so auf dem Screen sehen, ob er mehr neue Wareneingänge oder mehr freigegebene Kostenvoranschläge hat und priorisieren, welche Arbeiten er zuerst durchführt: Reparaturen oder Analysen des Reparaturbedarfs als Basis für neue Kostenvoranschläge.
„Oder ob, wenn sowohl der Wert für den Wareneingang als auch der für die freigegebenen KVs hochgeht, ein weiterer Mechaniker eingesetzt werden muss“, ergänzt Herz.
Zudem wird die Durchlaufzeit eines Auftrags angezeigt – sowohl das Mittel des Jahres als auch der Durchschnittswert der letzten abgeschlossenen Kalenderwoche. Im zweiminütigen Wechsel mit dem Wareneingangsscreen wird eine Liste sämtlicher Serviceaufträge mit Servicenummer, Kunde, Modell, Datum des Wareneingangs und aktuellster Buchung angezeigt – sprich jeder Prozessschritt im Reparaturablauf sowie die Anzahl der Tage seit der letzten Buchung.
Durch Peakboard profitiert MUNSCH nicht nur von Zeitersparnissen wie Herz erläutert:
„Die Kollegen haben bei der Card-Board-Variante, über die wir vorher visualisiert hatten, den manuellen Aufwand bemängelt. Das Abschaffen der Mehrarbeit durch das Umhängen der Karten kam natürlich direkt gut an.“
Zusätzlich ist die Transparenz deutlich gestiegen.
„Wir sind jetzt einfach sichtbar in unserem Prozess unterwegs, was den Mitarbeitern ein strukturiertes Arbeiten ermöglicht, ohne erst in irgendwelche Listen zu schauen. Ein kurzer Blick auf den Bildschirm und sie wissen, wie es aktuell läuft.“
Auch in Sachen Außenwirkung leistet Peakboard einen Beitrag, wie Herz berichtet:
„Zu unserer Firmenphilosophie gehört eine saubere, aufgeräumte, strukturierte Werkstatt, in der wir auch häufig Handelspartner und Kunden begrüßen. Das große Display mit dem aktuellen Reparaturstatus sehen wir als perfekte Ergänzung des positiven Erscheinungsbilds unserer Werkstatt. Wir erleben bei den Besuchern der Werkstatt immer wieder einen kleinen ‚Wow-Effekt‘.“
In Zukunft nur noch mit Peakboard
Die Schwestergesellschaft MUNSCH Chemie-Pumpen GmbH plant, künftig ebenfalls Peakboard für die Prozessvisualisierung einzusetzen.
„Ich habe am Tag vor meinem Urlaub den Bildschirm am Vormittag aufgehängt. Am Nachmittag hatte ich schon einen Kollegen im Büro stehen, der für seine Abteilung auch Peakboard nutzen wollte“, so Herz abschließend.
Starte jetzt mit Peakboard und vereinfache deine Prozesse
Verwandle Live-Daten in smarte Entscheidungen – mit Peakboard.